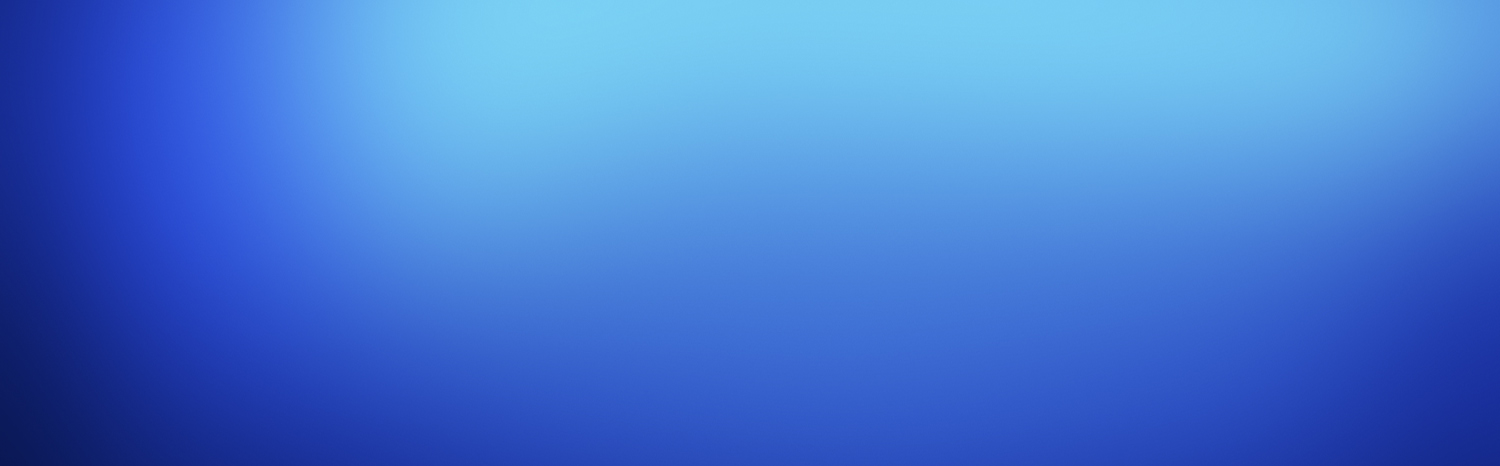
Using advanced design and manufacturing techniques that enhance affordability and product quality, Boeing has completed the detail design of major forward fuselage components for the two Joint Strike Fighter (JSF/X-32) demonstrator aircraft. Fabrication of those components is now underway.
"We've known from the outset that the development of this aircraft requires an innovative approach to both design and production," said Frank Statkus, Boeing vice president, general manager and JSF program manager. "The fabrication of the X-32 forebody components exemplifies the Boeing ability to leverage emerging military and commercial technologies and processes to affordably meet the needs of tomorrow's warfighter."
One X-32 forebody component, the inlet duct, is being fabricated as a one-piece composite structure using automated fiber placement technology developed by Boeing Phantom Works. The tool for the inlet duct is complete and fiber placement is well underway in St. Louis.
"Our fiber placement process allows us to produce large, composite structures better, faster and approximately 40 percent cheaper than we could with traditional approaches," said Jerry Ennis, Phantom Works' vice president of the advanced manufacturing, prototyping and produce processes.
Major components of the X-32 forebody include composite skins, several hundred machined parts, and aluminum frames currently being fabricated at the Boeing Space Center in Kent, Wash.
"The machining of forebody components in Kent embodies our design anywhere, build anywhere approach to JSF," Statkus said. "Having the ability to seamlessly integrate these leading edge technologies across our design team, regardless of geographic locale, contributes directly to the overall affordability of our concept."
To design, analyze and verify the forebody components, Boeing made extensive use of computer 3-D modeling and simulation technology, including virtual reality applications that eliminate physical mock-ups, time-consuming drawings and expensive test hardware. The same database is used for the automated numerically controlled machines that actually create the JSF parts.
According to Ennis, employing advanced technology cuts design and prototyping costs in half, and is used equally for tooling, manufacturing and maintenance concepts, as well as airframe and systems components. The eight-piece mandrel used for placing composite fiber against the inlet duct tool, for example, was designed with this process and the pieces "fit together like a glove," Ennis said, adding that "the rest of the X-32 fuselage will come together that way as well."
Final design, fabrication and assembly of the X-32 forward fuselage components will be completed in St. Louis prior to shipment to Palmdale, Calif. Assembly of the two X-32 forebodies is scheduled to begin in mid-summer. Boeing plans to assemble the center and aft fuselage sections in Palmdale, where mating with the forebody, final assembly, checkout and first flight of the two demonstrator aircraft will occur.
Phantom Works is supporting the Boeing JSF effort as the advanced research and development unit of the company's Information, Space and Defense Systems group. It specializes in finding innovative solutions to its customers' design, manufacturing and systems challenges.
Boeing is competing to build the JSF under a four-year Joint Navy and Air Force concept demonstration phase contract awarded in late 1996. The company is building two X-32 demonstrator aircraft while defining the characteristics of the operational aircraft - the Preferred Weapon System Concept. One X-32 will demonstrate characteristics of the Air Force's conventional takeoff and landing variant and the Navy's carrier variant, the second will demonstrate the short takeoff/vertical landing variant envisioned for use by the U.S. Marine Corps and the U.K. Royal Navy. A competition winner will be selected in 2001.
98-57